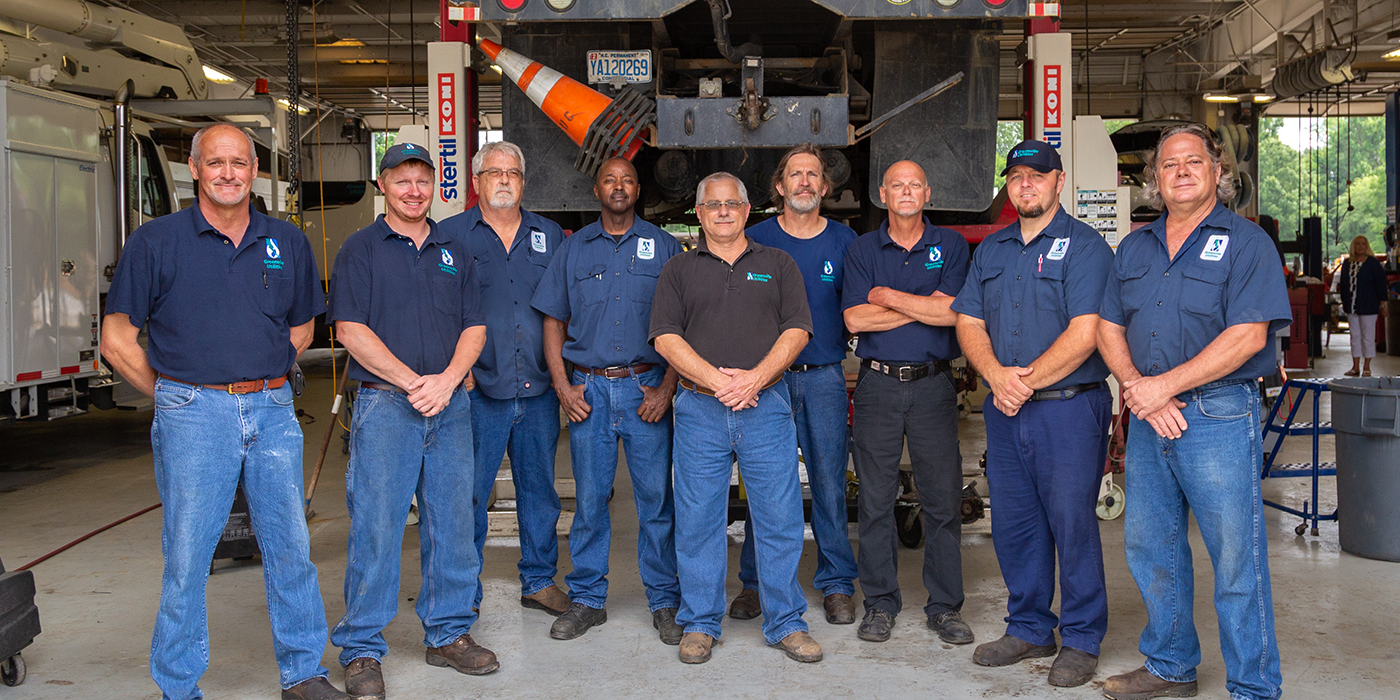
This month, we continue our departmental features with Fleet Maintenance, a section of the Finance Department.
There are many images our customers associate with Greenville Utilities, and one of the most visible is our fleet of vehicles and equipment. Employees in the field wouldn’t be able to do their jobs without our trucks, trailers, and equipment being kept in top-notch shape by the hard work and dedication of the employees in Fleet Maintenance, also known as the Garage.
Fleet Manager Billy Moseley directs the daily activities of our full-service garage that includes fabricating, welding, testing (diagnostics), inspecting, performing minor body work, and more. Billy and his team of 12 are responsible for 270 vehicles (from pickups and SUVs to bucket trucks), 283 pieces of equipment (from chainsaws to bulldozers), and 130 trailers.
Staff Support Specialist II Carol Colville maintains all Garage records. She also helps Billy manage the fleet maintenance programs, plate inspection purchases and scheduling, insurance adjustors, staff recertification, fleet replacement schedules, and other projects as needed.
Parts Manager Ben Gibbs maintains the Garage inventory by coordinating the purchase, stock, and issuing of shop parts, including oil inventory. He also assists Billy with monitoring our on-site fuel system and making sure we’re in compliance with the North Carolina Department of Environmental Quality.
Mechanic Supervisor Mike Adams oversees the daily operations of the shop and the Master Mechanics. Our Garage has a staff of Master Mechanics with over 75 years of combined experience and factory training in the field of automotive and diesel diagnostics and repair. This team includes Jerry Adams, John Britt, William Cooley, Kevin Lockamy, Kenneth McDonald, Ronnie Staton, Simon Stroud, Donald Wilson, and Kenneth Wrenn. They are responsible for the routine maintenance and servicing of GUC’s fleet, which also includes “in servicing” of new vehicles and equipment (logo decals, safety outfitting, etc.).
Like many other teams at GUC, Garage employees are versatile and cross train as much as possible; however, they do have their specialties. For example, some might be called on more often for their expertise with bucket trucks, while others might work more with welding and fabrication (modifications to vehicles like battery tamers and pipe racks). Whatever their specialties, our Mechanics work well together to not only take care of the daily needs of our growing fleet, but to assist crews with unforeseen issues that arise when out in the field or on out-of-town emergency mutual aid events. Like our crews, Mechanics also get the occasional after-hours call.
Since GUC has a variety of fleet needs to service four different utilities (electric, water, sewer, and natural gas), our Mechanics are required to get a range of certifications in specialties; from Altec bucket trucks and Ford diagnostics to compressed natural gas vehicles (to name a few).
Fleet Maintenance has grown tremendously as GUC has grown. Our Garage employees have been able to refurbish both old and new vehicles to fit the ever-changing needs of our crews. As a result, our vehicles are servicing the needs of our employees and customer longer.
Next up, we’ll cover the Safety Office, which will wrap up the Spotlight On Finance series.